The Smart Car Bed for Clifford is finished!
Wahoo! It's been a long time coming but definitely worth the wait. I drove down to the welding shop in the Smart car, loaded it onto the bed by driving up the ramps and then drove home with $PRITE on the bed.
Lots to tell and it will likely take some work before I get it all documented in the way that I would like.

The
bed design as previously documented is very simple. I had several points that I wanted to be clearly achieved:
- Simple design that could be built by a decent welder and a hands-on owner
- Drive on / Drive off system to eliminate complexity and limitations
- Full fender protection for all tandem tires to prevent possible car/trailer damage should a tire blow or a big rock get thrown by the tires.
- Use the existing commercial hitch with future option of air ride hitch
- Good tire traction during loading and unloading of the car
- Simple but secure tie down for the car. Make it easy access to lash it down for travel
- Bed should have easy access to most of the under-bed truck chassis and parts.
- Easy around the rim tie down lip for carrying other "stuff" on the bed.
- Aesthetically looks like it fits the truck and is not some hack job adaptation.
- Predictable expense to build it.
I am very pleased that we have achieved all of these objectives. Full resolution albums of the bed design and build are located on my
Rvbuddy.smugmug.com/RV-Full-TIming photo site.
Below, I will try to provide a little depth to each of these points:
1 Simple Design
- The bed frame is all built out of 2” x 3/16” steel angle iron with a few 2”x2” reinforcing steel tube stringers for stability.
- It sits on 3”x5” Steel tubing rails that sit on top of the truck frame rails with a 1”x3” white oak strips that allow some flex of the frame without damaging the bed. The steel tubing is fastened to the frame rails by 6 U-Bolts and 2 steel flanges are welded to the sides of these tubes to prevent any rotation or side slipping of the bed on the rail in extreme conditions.
- The loading tracks use the original cat walk sections to both raise the tires and to provide traction and drainage.
Gaps are left at each end to accommodate standard rubber truck tire chocks as end stops during loading and unloading. - Tire to fender clearance was set to 1” when the air bags are deflated.
- Additional flexible mud flaps will be added to the bottom edge of the fenders to reduce throw back from the tires.
- Most welds are full width of the contact points and done on all sides where contact occurs.
2 Drive on / Drive off system
- The ramps are rated @ 2000 lbs and designed to be used separately or clamped together to make a single 38” wide ramp for loading/unloading motorcycles and/or ATVs or other “Stuff”. The rungs of the ramps are sharply grooved to provide better traction.




- They are 12’ long with a 12 degree bend at the middle hinge point to reduce the break over angle when the car comes over the edge of the bed and off of the ramps. This has been a big issue with loading/unloading
- The ramps fold to 6’ each and each weighs about 55 lbs
- They are supported on the edge of the bed by a one piece flange that is pinned to the deck with drop bolts to prevent any movement or slippage. In this example, I was unloading onto an uneven raised hill so the ramp tangs did not seat in the mounting strips properly but the bolts pinned through the ramp and the mounting flange still kept the ramps solidly in place.

- Space was designed in so mirror contact of the car and the truck faring would not be a problem regardless of the direction of loading or unloading.
- Ramps are each 19” wide so there is some room for slight corrections.
- The ends of the 2”x2” square tubing that borders the tire tracks was left open so that a winch setup could easily be added, if desired. Some folks want to winch, others don’t but I am sure that there will be times for us that winching will be preferred and if so, that option will be available with a slide in support frame.
3 Full fender protection

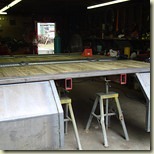

3/16” steel plate welded between 2”x3/16” steel angles make these fenders very protective of the car and the trailer should a truck tire separate or road debris get picked up in or between the duals and thrown an any direction.


The bed is made 102” wide to give more overhang on the sides for the tandems for better protection.
4 Use Existing commercial hitch
A debate has long raged about using commercial hitches to pull RVs. Evidences exist on both sides proving their position but an air ride hitch is a very significant additional cost to some people and unless it is the right one, may not make any difference in the end.
Pounding of the RV pin box by the hitch is seen as having a very big potential for damage to the RV frame integrity. Some RVs can handle it and many can’t and start to have metal fatigue points in the structure.
My own view is that vertical pounding is only one of the forces at work to do such damage. Probably more damaging is the starting and stopping forces that the RV pin box may get when being controlled by a Heavy Duty Truck (HDT). Good driving techniques are, therefore, more important than hitch design in moderating these forces.
As for the vertical pounding, running tandem axles on the truck with 4 air bags inflated to less than 20lbs/sq in allows some absorption of these types of forces. Also, running duals doubles the tire contact areas thus often spanning potholes and bumps with a parallel tire. The tandem axles span wide road artifacts, like rail road crossings, dips and speed bumps and give more of a “crawling over it” dynamic to it. This can easily be seen when crossing a speed bump in a parking lot. The front axle bumps up over it and the rear tandems crawl over the same obstacle with much less vertical displacement thus “softening” the experience.
Another big concern is the single plane of articulation that a typical commercial hitch is limited to. It can tip forward and backward to accommodate vertical changes in truck-trailer angles but it cannot tip side-to-side to handle uneven surfaces, such as in some campgrounds and roadside areas such as entrances to service stations, campgrounds, etc.
There is a certain amount of play in the kingpin-hitch interface and there is a bit of flex in the design of any well built RV. The problem is where does the stress go when the truck and trailer are being “twisted” relative to each other. The truck frame is designed to twist…. some but that is expecting a lot more than the typical 3000 to 5000 lbs of a typical 5th wheel RV pin weight. It is certainly something to be concerned about for the long term integrity of the RV.
Would I like an air ride hitch, sure.. if it has enough throw range and damping to significantly reduce these forces in typical towing… and if I can ever afford one, I will get it. Some feel it is cheap insurance compared to the costs of fixing a cracked RV frame and I don’t disagree.
5 Good tire traction for Smart
The original design was to have the tire tracks in the bed made out of 3/16” diamond plate. Some serious thought was also given to adding expanded mesh over flat plate but each still left me with a problem of buildup of ice or mud or tree trash in these tracks which could cause tire slippage during loading or unloading.
I chose to look at using the catwalk sections from the truck with their very open but aggressive surface design to fit in the bottom of these tracks.
They are 1” thick and help reduce the break over angle at the edge of the bed. Separating them into the sections to fit was not hard and then they were bolted down to the bed frame.
Space was left at each end of the traction sections to drop in a standard rubber wheel chock with a lip to prevent it from getting pushed off of the edge of the bed during loading.
These are already in use for chocking the truck and trailer tires so they are not additional stuff to carry.
6 Secure tie down for the car
Various folks have used various means to keep their smart car in place on the bed. Some have worked better than others and some have just not “failed” yet.

I use webbed tie down belts with strap baskets to insure the belts stay on the tires no matter what. These are the same commercial basket belts that tow trucks use for much bigger and heavier stuff.
To actually hold the tires under pressure, 4 load binding winches for flat bed semi trailers are used. Instead of being welded to the bed (or under it as in the original design) they are slipped in under tabs that keep them in place but allow some sideways movement during tie down to accommodate where the individual tire may be sitting in the tire track.


The front and rear tires have different track widths on the Smart and this was a concern for centering the tie downs for maximum security on each tire regardless of the side used to load it onto the Smart bed.
The webbed tie downs are designed so that they can be secured with an offset to the center of the tire and still not have any risk of coming off.
This lets them align easily with the load binder winches as needed.
Between the sideways adjustability of each load binder, the length of the slot for the strap and the way that the straps tighten up on the tires, a lot of tire offset can be accommodated.
Watching them being removed before unloading gives some perspective about how they hold the smart car down and how they work.
7 Easy access to under bed truck parts
For me, this was a really big item. I try to do as much wrenching as I can for maintenance and repair. Most truck beds completely obscure access to what is under them so full access is usually a matter of having a truck lift, a service trench or removing the bed with a hoist or fork lift. Out on the road, none of these are options without first having a tow to the right shop.

Designing the bed to be 2” x 6” wood decking that is retained in place by a flat steel strip on each end, allows easy access to any part under the deck just by loosening or removing 6 bolts and slipping the boards off and out of the way.
For cost, salt treated lumber was used but if I ever find myself where white oak 2” x 6” lumber is cheap, it will replace the decking in a heartbeat.
8 Easy hook bed edge for tie downs of “stuff”
I had envisioned a 1” x 1/4” steel strip to be welded around the bed with spacers to have a convenient edge to hook tie downs to but the 2” x 3/16” steel angle iron that supports the perimeter of the bed eliminated the need for that so this is even simpler.
9 Aesthetically acceptable to look at
Though these are only numbered for reference this item is near the end of my requirements because it takes what it takes to satisfy the requirements of physics and safety and whatever is left available usually does not leave much room for aesthetic adjustment.
In this case, it came together with all of it intact and, to my eye, looks very natural. It is subtle but present and integrates nicely with the truck cab and faring. Looks like it could handle a “woody” stake side added, just for looks.
10 Predictable cost to build.
Actually, not that predictable! The steel came in at about $1900. The welding work (as estimated by others) was expected to be under 10 hours. In reality, it took about 100 hours but that included not only the steel work but all of the wood work, painting (2 coats of primer and Black glossy epoxy) and “figuring “ that it took to solve some of the issues “in flight”. Up front, Scott was more realistic about the unknown time and effort it would take and just gave me a flat rate/hour. My own expectations of how many hours it should take were in error. The estimate for the steel was obtained prior to my committing the work to be done.
The company, Flores Welding, does steel fabrication over much of the southeast US. Russell, the fabricator that did this work, has been doing this for over 18 years and had some impressive examples of his work. Scott Holland is the lead estimator and did some of the actual work along with solving some of the problems and issues that came up. Together, they made it happen right.
All in all, it totaled about double the cost I was realistically expecting. Prior to this I was unable to get anyone to give me a firm estimate of costs to plan around but in the end, I got exactly what I really wanted, the way I wanted it.
Even though this was a first-off one of a kind, there was no throw-away material and no re-cuts due to errors or unanticipated issues during fabrication. What was cut and welded stayed welded.
I could have shaved some of the costs off by providing some labor myself. I had originally intended to do this but a combination of things including the weather, made this much harder to do that I had hoped. The shop was about 40 minutes away and this is in Central North Carolina going into the summer months and I am just not any good in the heat.
I could also have done some things, like all the unbolting and bolting, some of the drilling and the decking work and painting. When I saw how well Russell worked I just woosed out and let him do his thing and I am very glad I did.
Probably the biggest reason I didn’t work on it at the shop was that everyone there smoked and I am allergic to tobacco smoke, big time. I would have liked to have hung around during the work a lot more. They were very agreeable to my assisting but there was more than once that my allergies took me out of service for a couple of days after a short visit to take progress pictures.
All in all, would I do it again? Absolutely! I would just plan on it costing a good bit more on the top end than I had anticipated. I don’t think that I could have gotten a better job anywhere else at any price and I am sure that several of the places that I did attempt to give the job to would not have done anywhere near this quality nor completeness.
Now that these guys have built one they know what it will take in time and materials and I am certain that they can fabricate more of these in less time. They did say they were interested in building more of them and there is a full RV park less than a mile up the road from their shop. While it is not a resort, it is very convenient to the job site and only a couple of miles off of I-40 in Garner, NC should anyone be interested in dropping by and checking out the shop.
I am a happy camper!